Línia de granulació de flocs d'ampolles de PET
Pelletitzador de reciclatge d'ampolles de PET Màquina de granulació PET Flux de procés
Alimentador al buit → Assecador de cristall d'infrarojos → Descàrrega al buit → Extrusora d'un sol cargol → Bescanviador de pantalla hidràulica → Capçal de la matriu de refrigeració per aigua → Abeurador de rentat d'aigua → Granulador de rentat d'aigua → Màquina de deshidratació → Màquina de tamís vibrant → Embalatge del producte acabat.
Especificació tècnica
Nom de la màquina |
Línia de pelletització d'extrusió d'un cargol PET |
Matèria Primera |
Flocs de rPET |
Producte Final |
Pellets rPET |
Components de la línia de producció | Sistema assecador de cristalls infrarojos: Alimentador al buit / Assecador de cristalls infrarojos / Descàrrega al buit
Línia de granulació d'extrusió d'un sol cargol: Extrusora principal d'un sol cargol / Canviador de pantalla de doble pistons hidràulic / Capçal de matriu / Abeurador d'aigua / Pel·litzador de rentat / Màquina de deshidratació vertical / Màquina de tamís vibrant / Emmagatzematge
|
Diàmetre del cargol |
90 mm-150 mm |
L/D |
1:24/1:30 |
Interval de sortida |
150-1000 KG/H |
Material del cargol |
38CrMoAlA amb tractament de nitració |
Tipus de peletització |
Rentat i peletització d'aigua |
Canviador de pantalla |
Canviador de pantalla hidràulic de doble pistons |
Detalls de la màquina
Assecador de cristalls infrarojos (DISENY DE PATENT DE LIANDA)
① La millora de les propietats físiques i de fabricació del PET reciclat de qualitat alimentària mitjançant la tecnologia alimentada per ones infrarojes té un paper crucial a jugar en la propietat de la viscositat intrínseca (IV).
② La precristalització i l'assecat dels flocs abans de l'extrusió ajuda a minimitzar la pèrdua d'IV del PET, un factor crític per a la reutilització de la resina
③ El reprocessament dels flocs a l'extrusora redueix l'IV a causa de la hidròlisi en presència d'aigua, i és per això que el pre-assecat a un nivell d'assecat homogeni amb el nostre sistema IRD pot limitar aquesta reducció.
A més, les tires de fusió de PET no es tornen grogues perquè el temps d'assecat es redueix (el temps d'assecat només necessita 15-20 minuts, la humitat final pot ser ≤ 30 ppm, el consum d'energia inferior a 60-80 W/KG/H)
④ El tall a l'extrusora també es redueix perquè el material preescalfat entra a l'extrusora a temperatura constant.
⑤ Millora de la sortida de l'extrusora de PET
Es pot aconseguir un augment de la densitat aparent d'un 10 a un 20% a l'IRD, millora substancialment el rendiment d'alimentació a l'entrada de l'extrusora; mentre que la velocitat de l'extrusora es manté inalterada, hi ha un rendiment d'ompliment substancialment millorat al cargol.
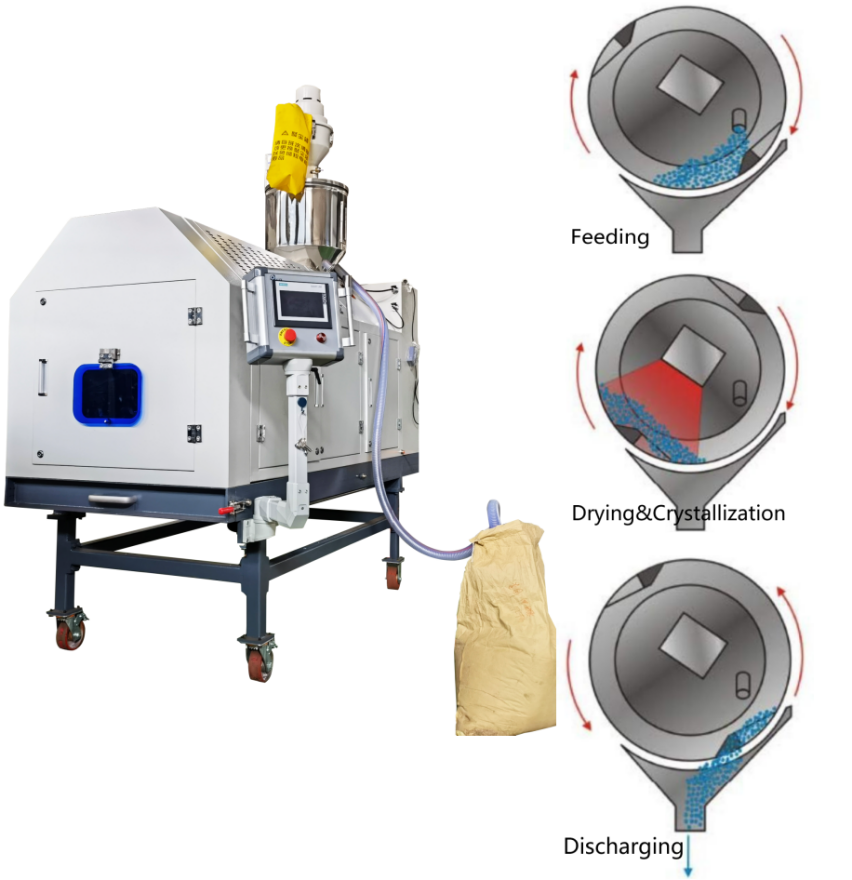
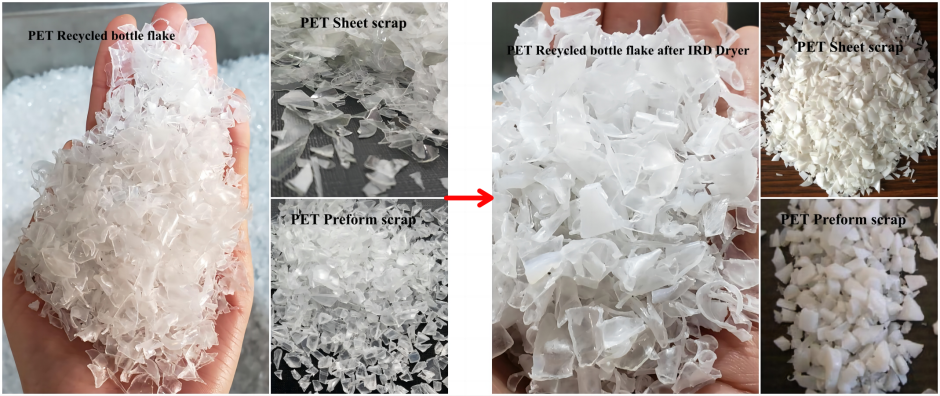
Línia de pelletització d'extrusió d'un sol cargol (sense ventilació al buit)
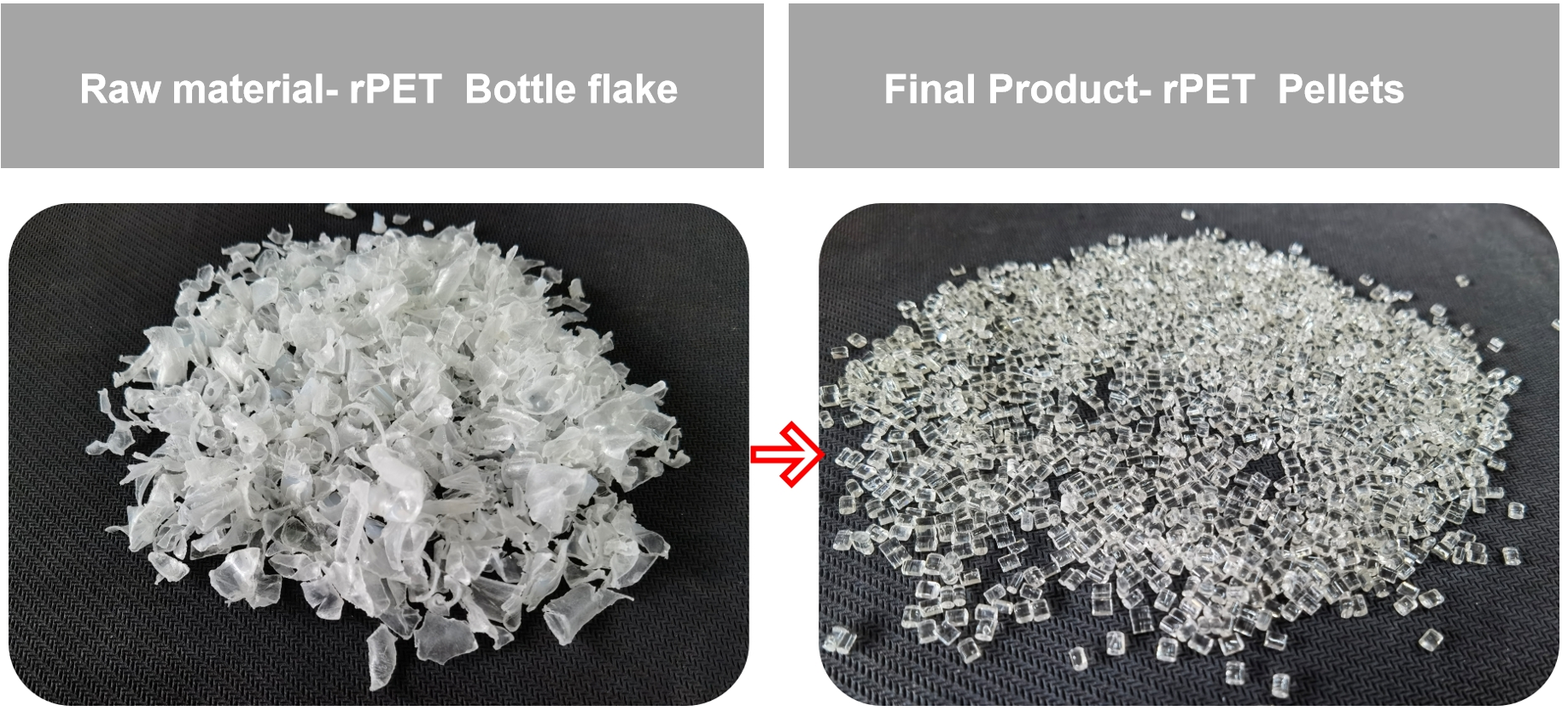
Utilitzant els punts forts de l'extrusora de cargol individual i emparant-lo amb un cargol dissenyat exclusivament LIANDA per a flocs d'ampolla rPET, vam poder augmentar la capacitat en un 20% amb menys energia consumida en comparació amb l'extrusora de doble cargol paral·lel.
Viscositat dels pellets de rPET produïts pel nostre sistema: només hi ha una caiguda de viscositat ≤0,02-0,03dl/g --- sense afegir cap potenciador de la viscositat. (Segons les nostres proves internes)
Pellets rPET Color: transparent --- sense afegir cap potenciador de transparència
Sense sistema de ventilació al buit --- Estalvi de costos energètics, treball estable i sense problemes
Fotos de la màquina
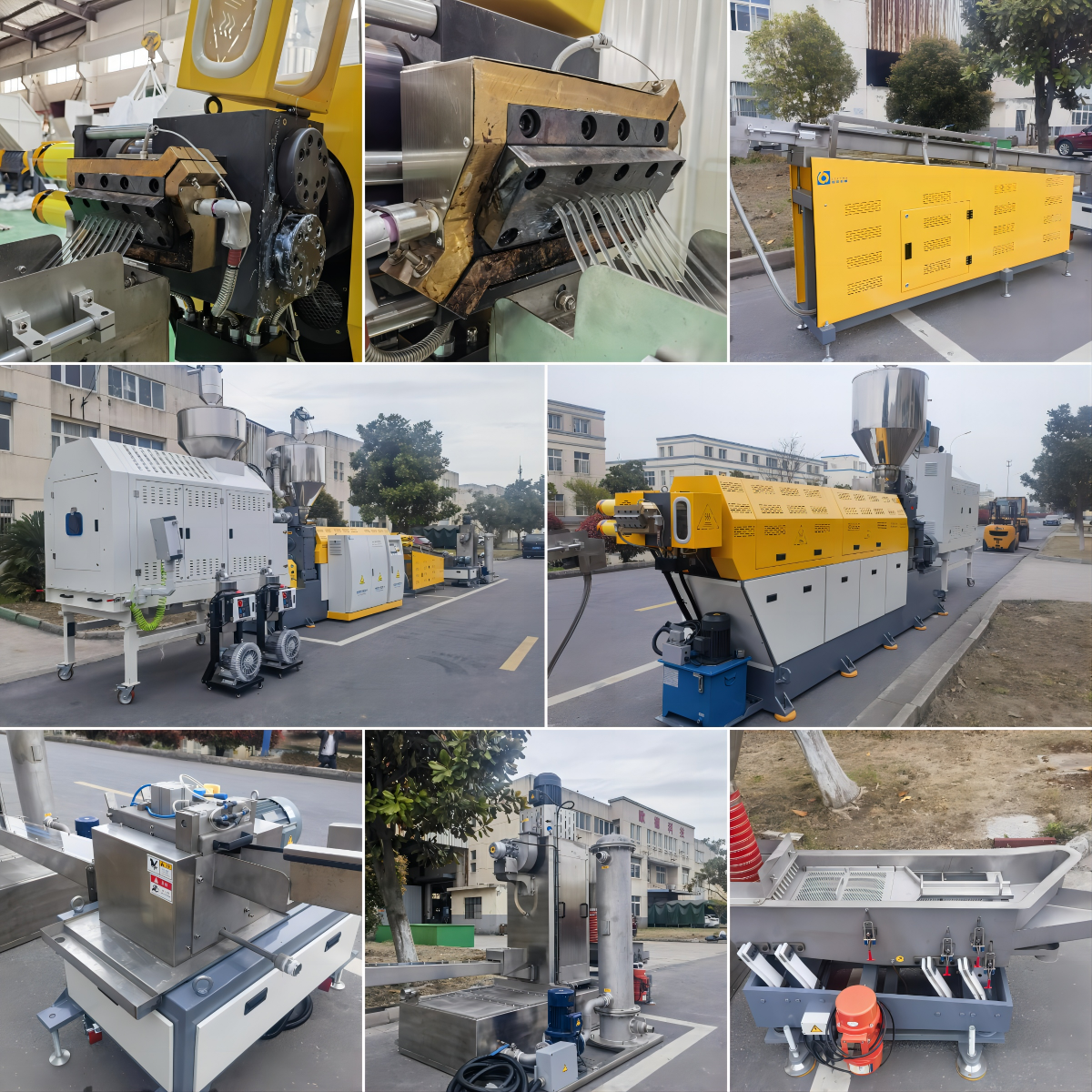
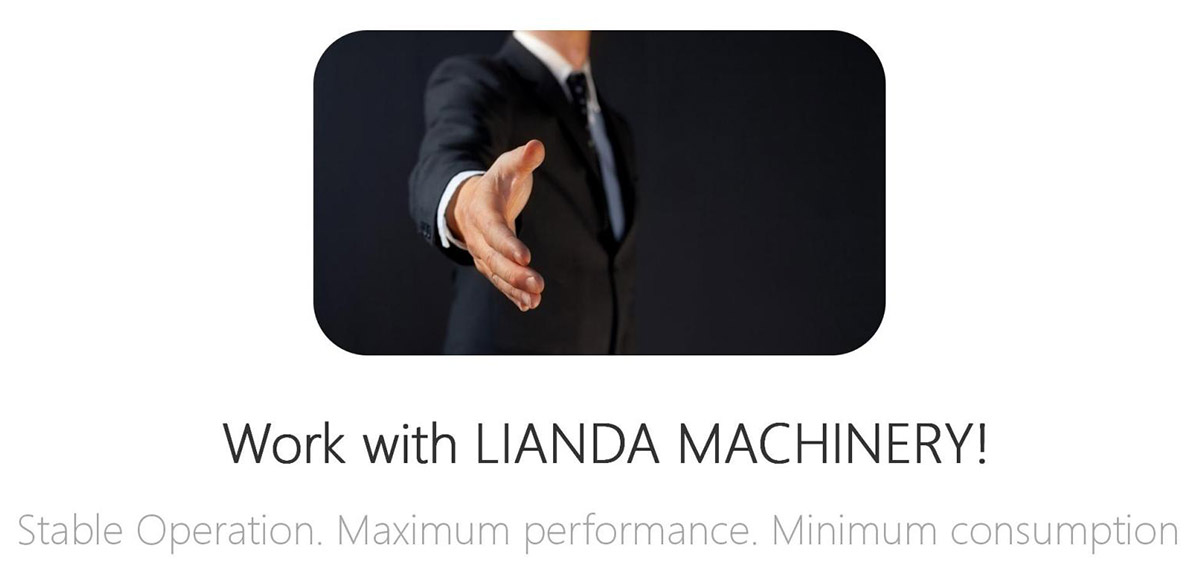